Superadobe Technique
At COCO SALVAJE, we prioritize innovation and sustainability. When designing our lab, we embraced the Superadobe technique, developed by Iranian architect Nader Khalili in the 1980s. This method uses long sandbags filled with earth, stacked in layers to form walls, and stabilized with barbed wire, creating strong, durable, and dome-shaped structures. Superadobe is low-cost, quick to construct, earthquake-resistant, and environmentally friendly. Plus, it looks super cool.
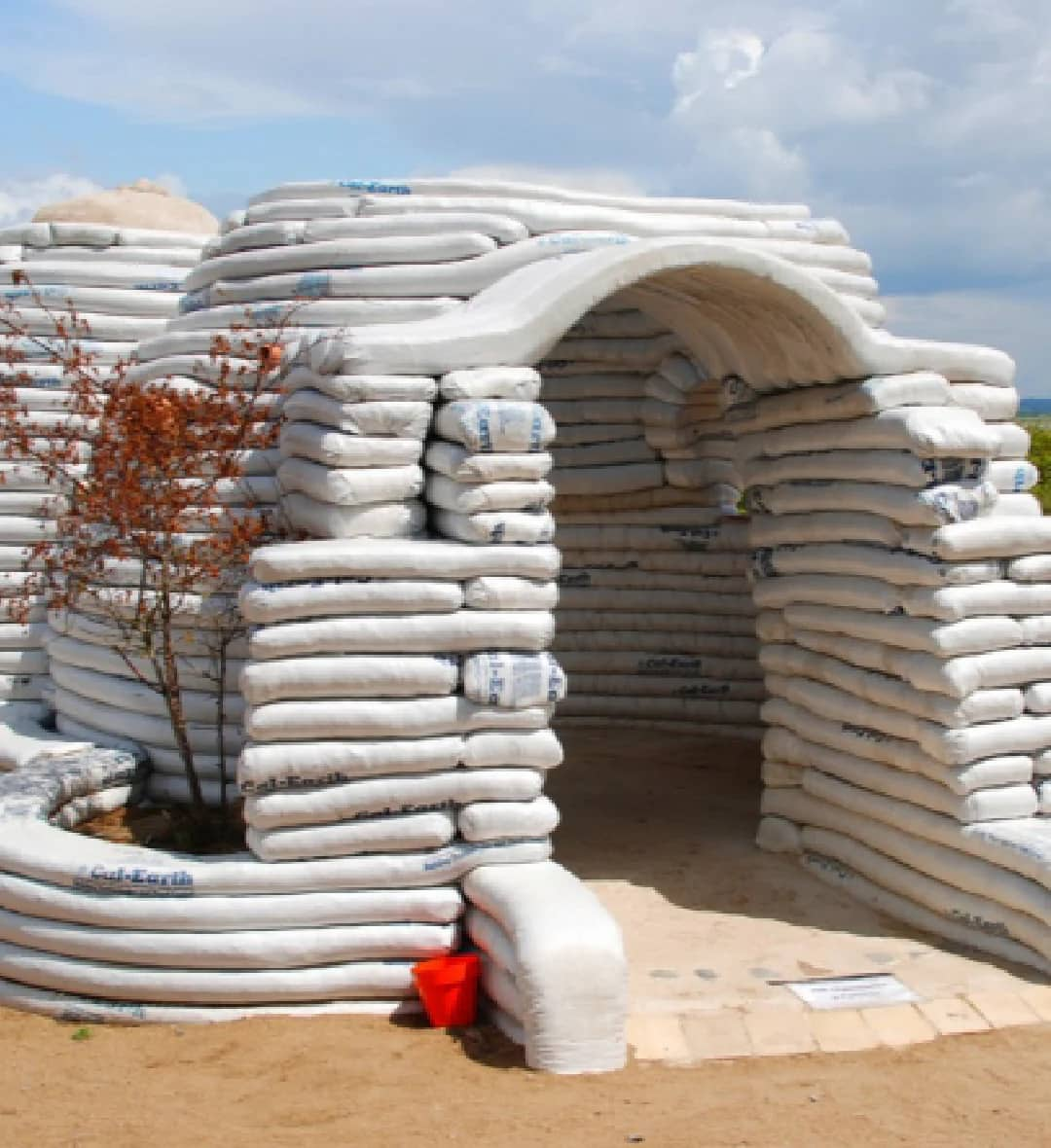
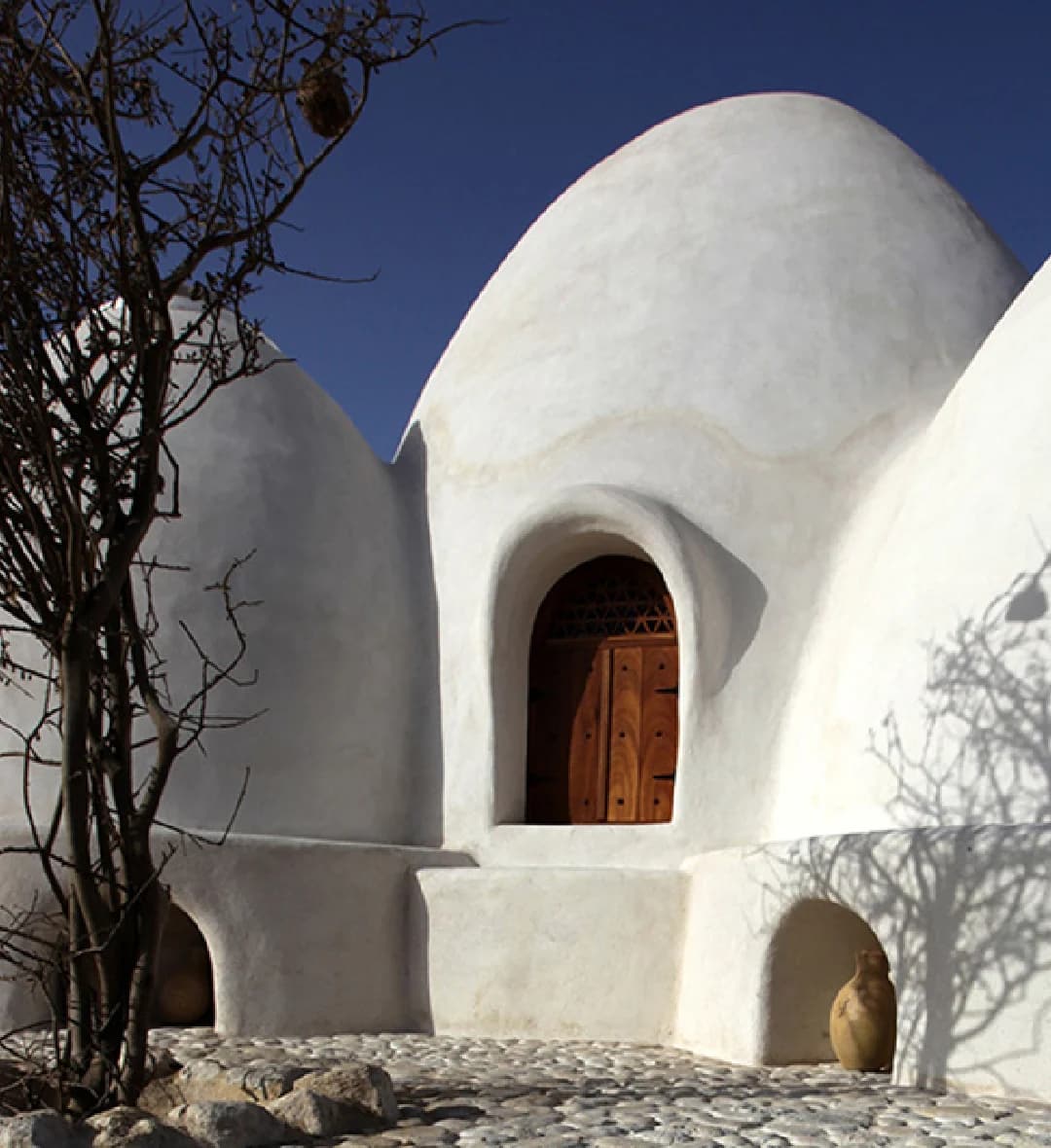
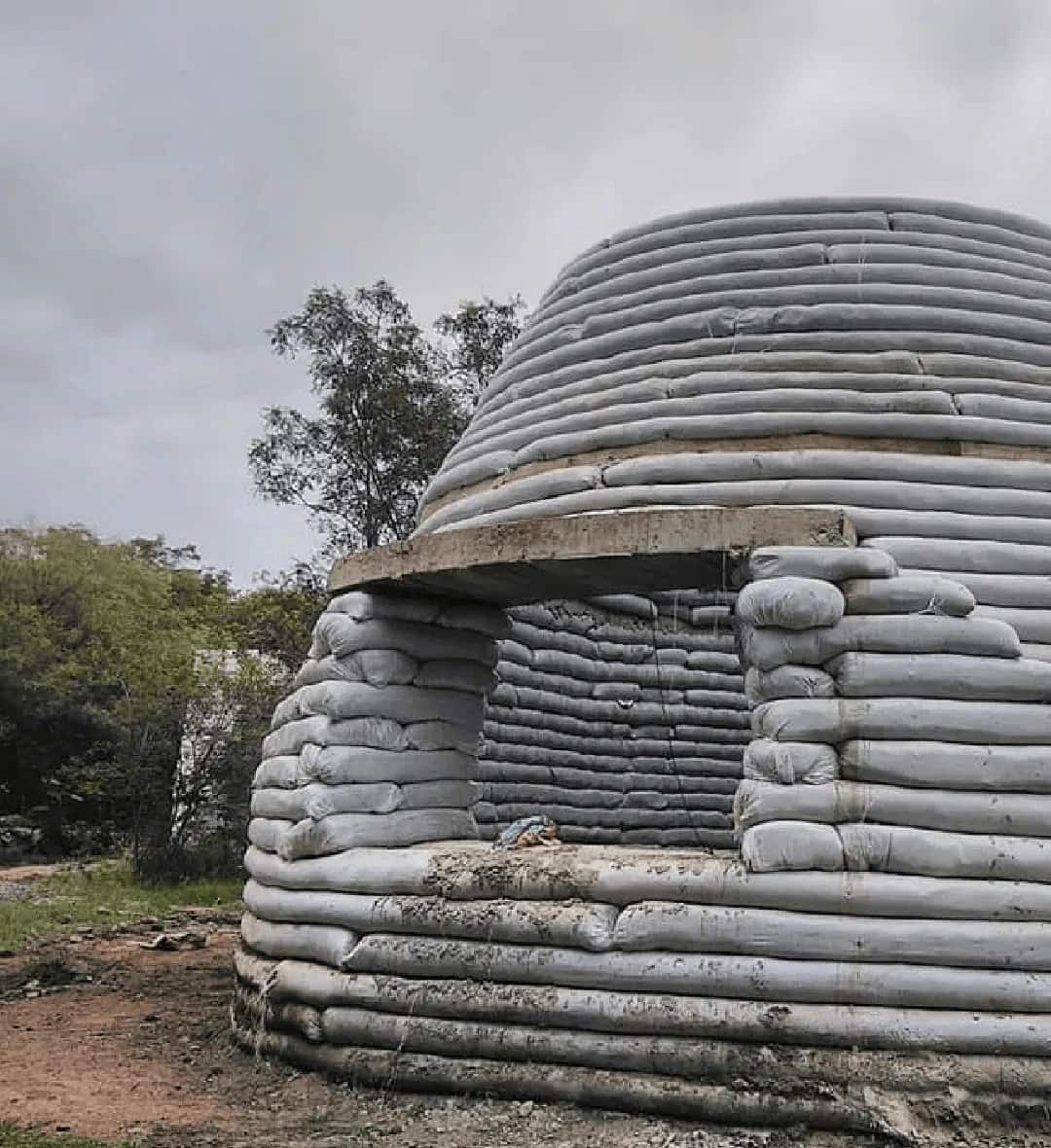
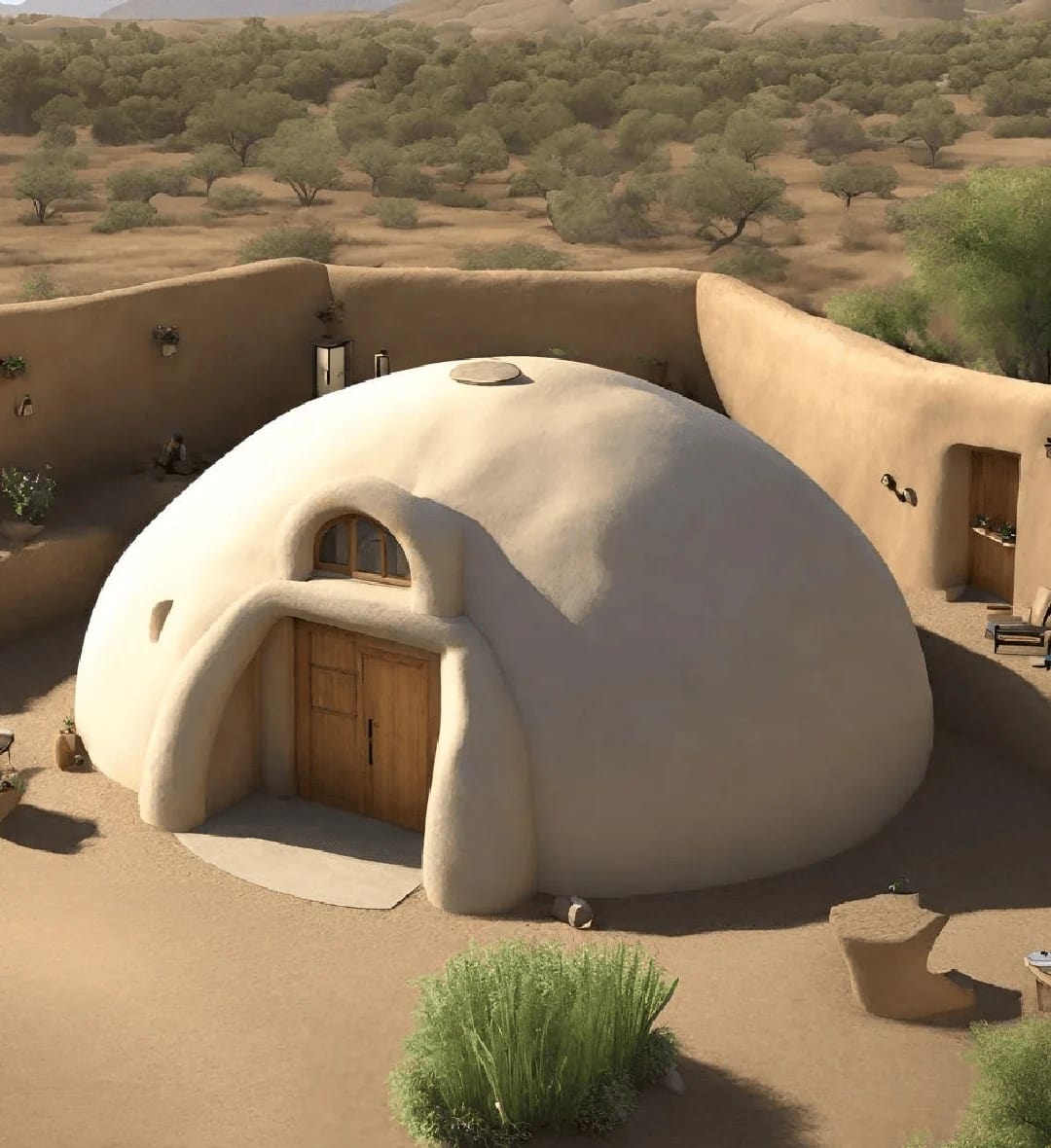
Why did we choose to build with Superadobe?
Low Embodied Energy
Embodied energy refers to the amount of energy required to produce and transport building materials. Superadobe has a low embodied energy because the materials used were sourced locally and do not require extensive processing or transportation.
Reduced Carbon Footprint
Superadobe can help reduce the carbon footprint of construction. This is because soil is a carbon sink, meaning it absorbs and stores carbon dioxide from the atmosphere.
Energy Efficiency
Superadobe structures are naturally well-insulated due to the thickness and density of the earth-filled bags. This can help reduce the energy required to heat and cool the building, making it more energy-efficient.
COCO SALVAJE'S LAB
We embarked on mastering the incredible superadobe building technique while ensuring compliance with Colombia's stringent sanitary regulations. Our journey involved assembling a remarkable team: a chemist elucidated the requisite spaces and their symbiotic relationships, a superadobe expert imparted construction wisdom, and an architect conceptualized the entirety of our space.
Collaboratively, we crafted a layout comprising two interconnected circular spaces—one dedicated to coconut oil production, the other to cosmetics. Linking them was a space crowned with a flat roof. This innovative design not only satisfied our hygiene standards but also yielded an aesthetically striking and operationally efficient environment for our manufacturing endeavors.
Our architect, Carlos Enrique Santamaria, faced the challenge of creating separate rooms for production, packaging, storage, quality control, and a transition area under one roof. Inspired by Oscar Niemeyer's Museum of Contemporary Art in Niteroi, Brazil, he incorporated a hexagon shape within our circular building. This design optimized space and centralized cosmetics production.
Originally envisioning a dome-shaped structure, we realized a 10-meter diameter dome would require an impractical 18-meter height. Instead, we chose thermoacoustic tiles for the roof, providing excellent insulation and sound absorption. We also added a flat space between two circles in the roofing for clients to view the sloths in the trees above the lab.
Construction was completed in six months, faster than traditional methods. The first three months focused on walls and roofs, while the next three months included plastering, building internal PVC walls, painting, installing custom stainless steel tables, and setting up the electrical system. Our space meets high sanitary standards with non-porous surfaces and meticulous documentation to ensure product safety.
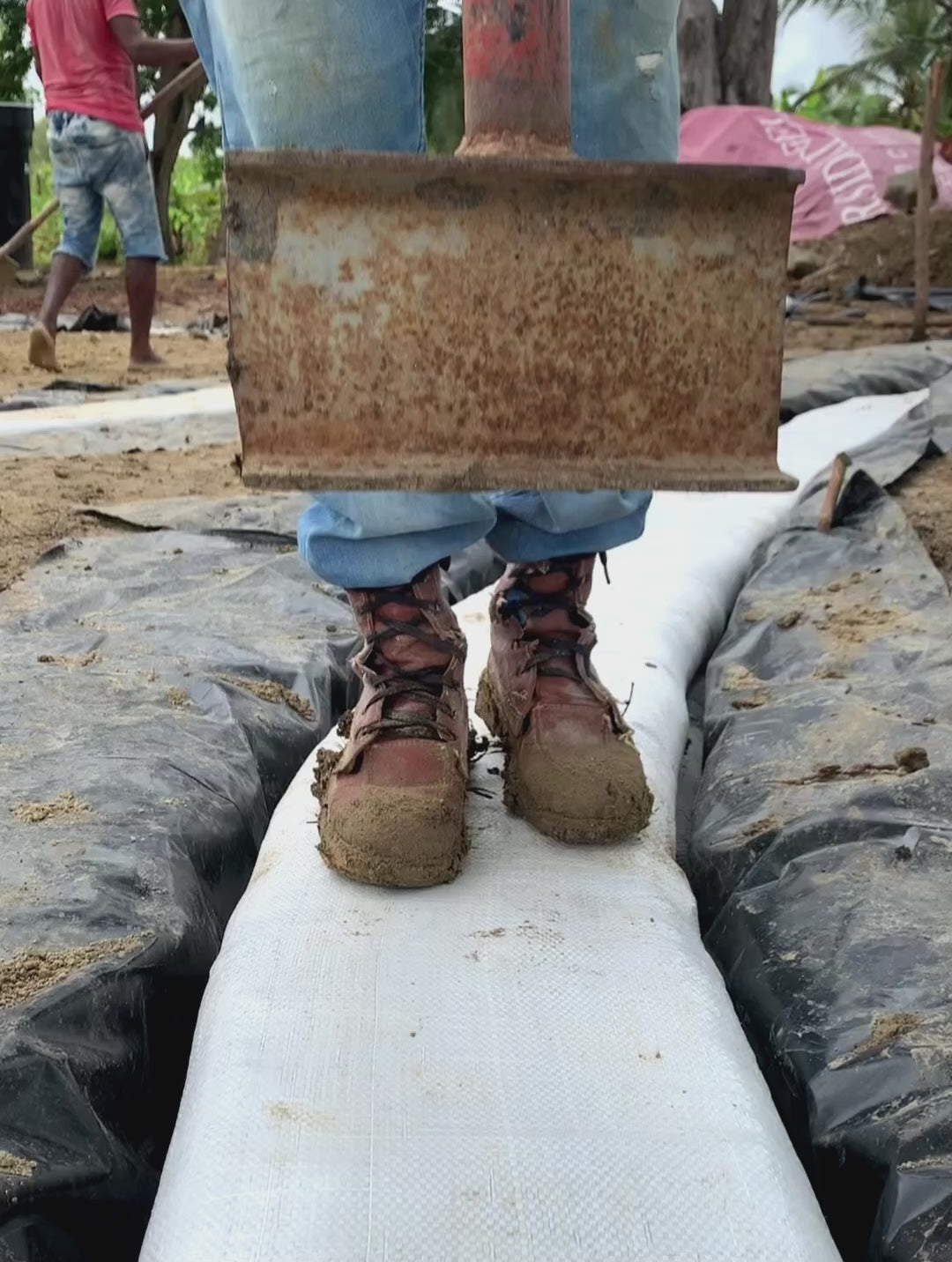
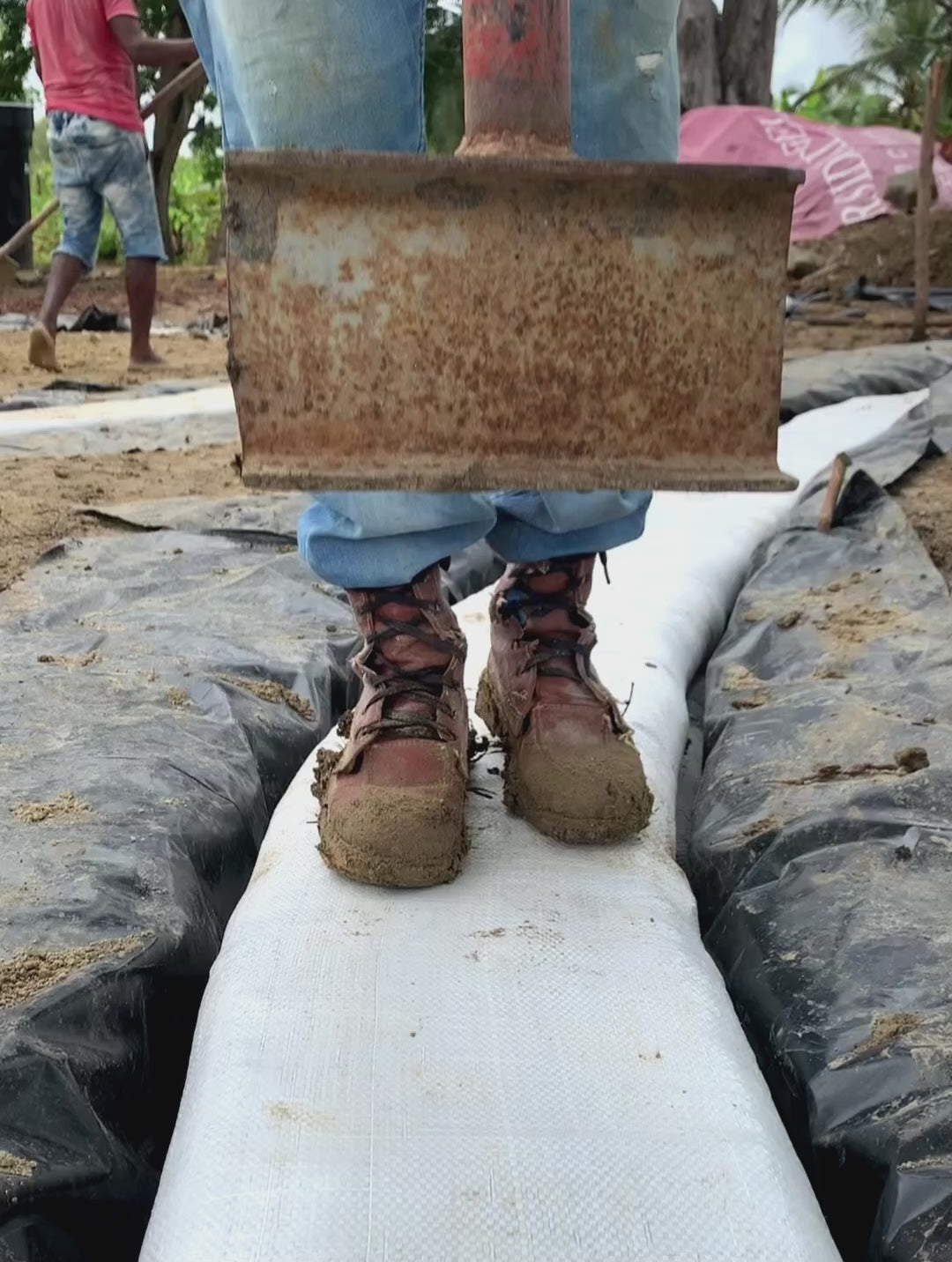
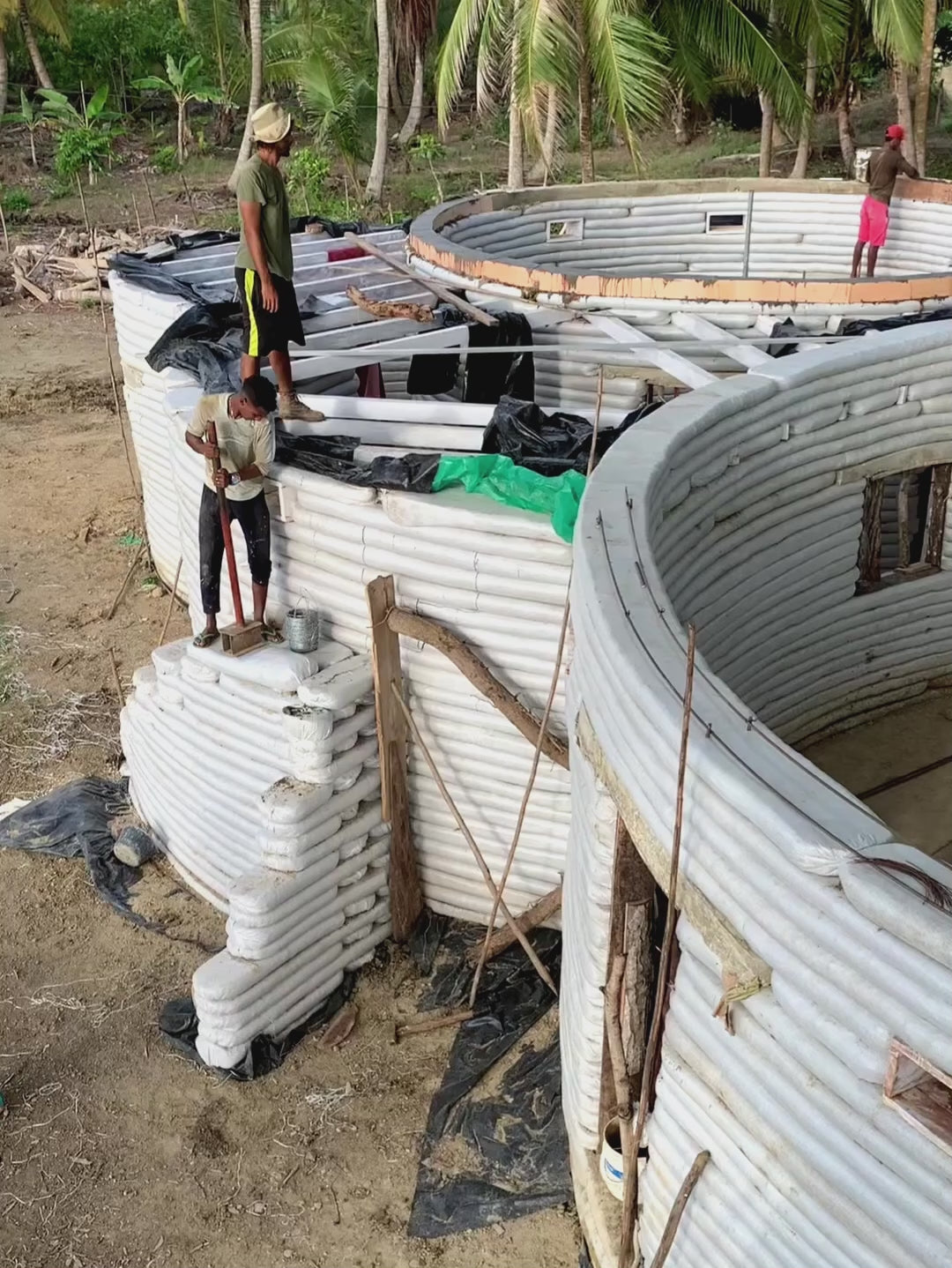
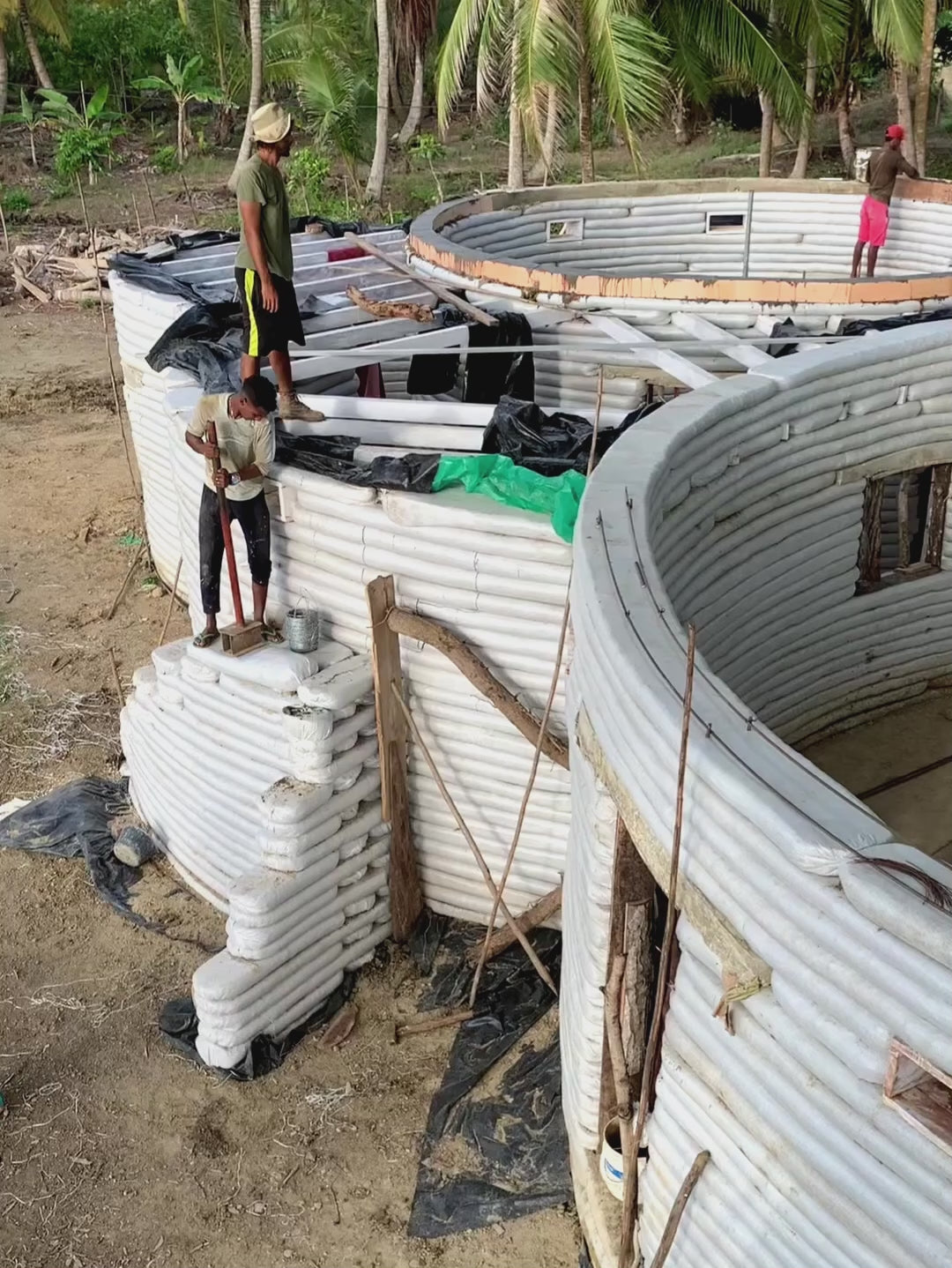
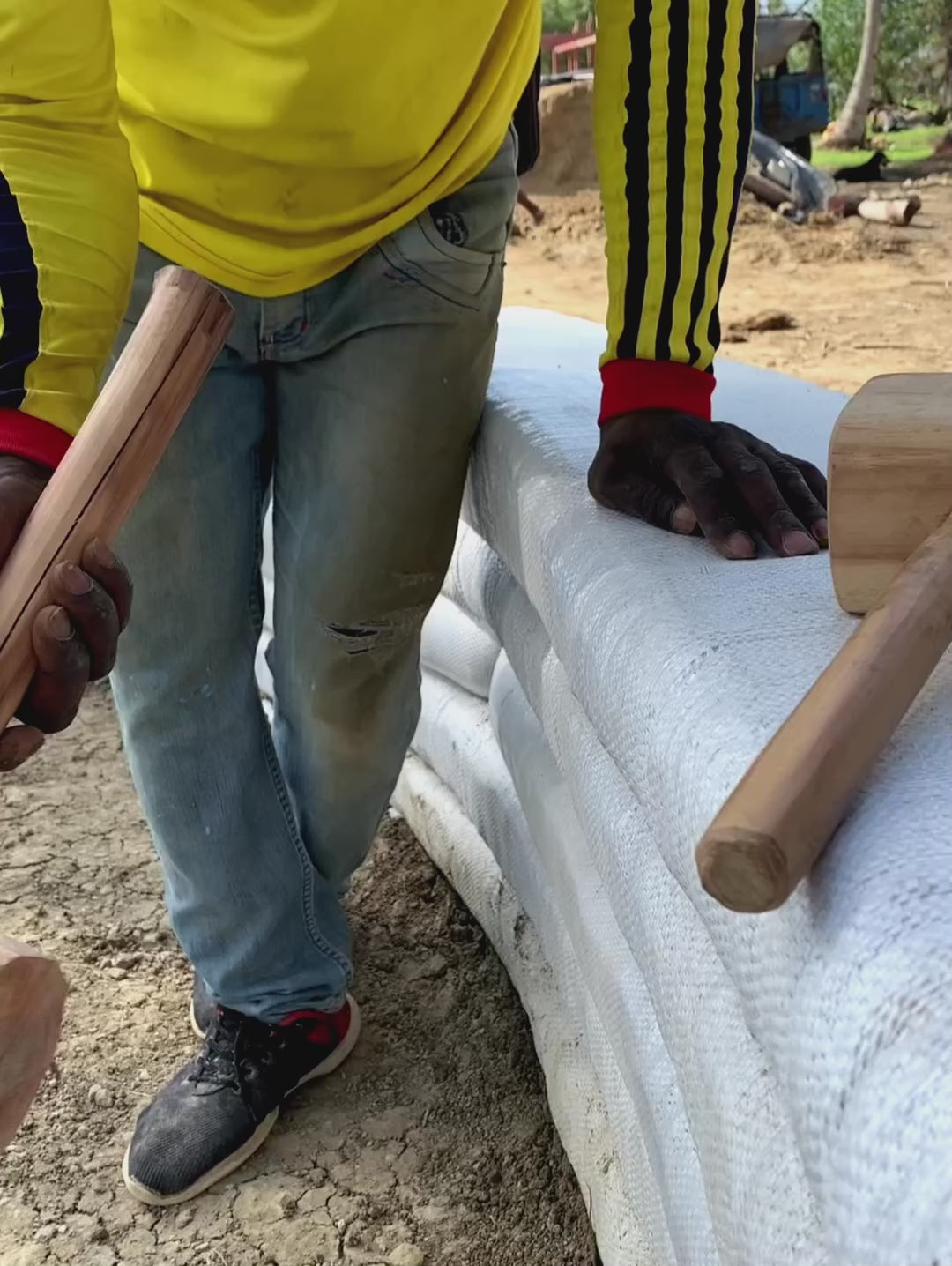
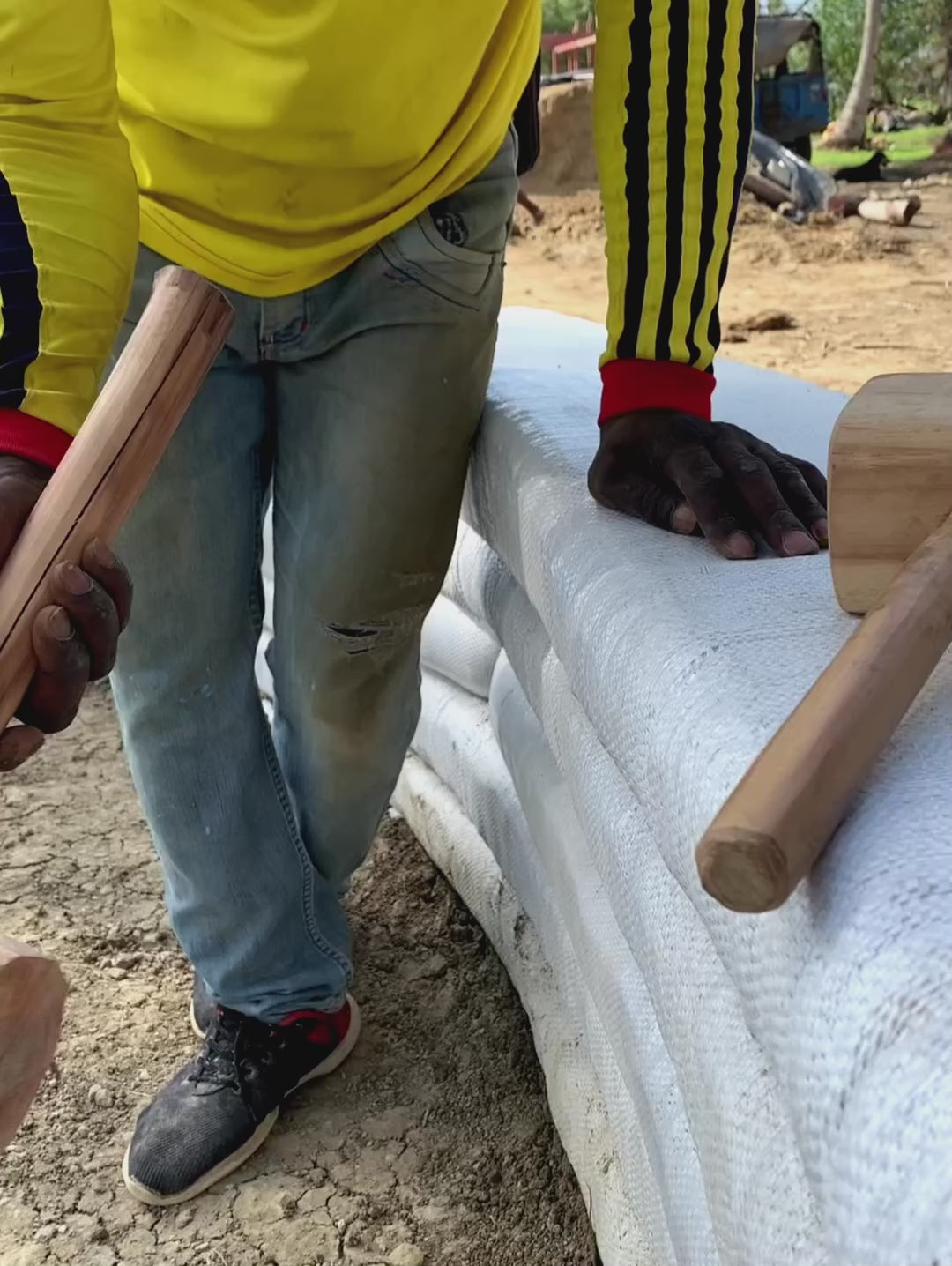
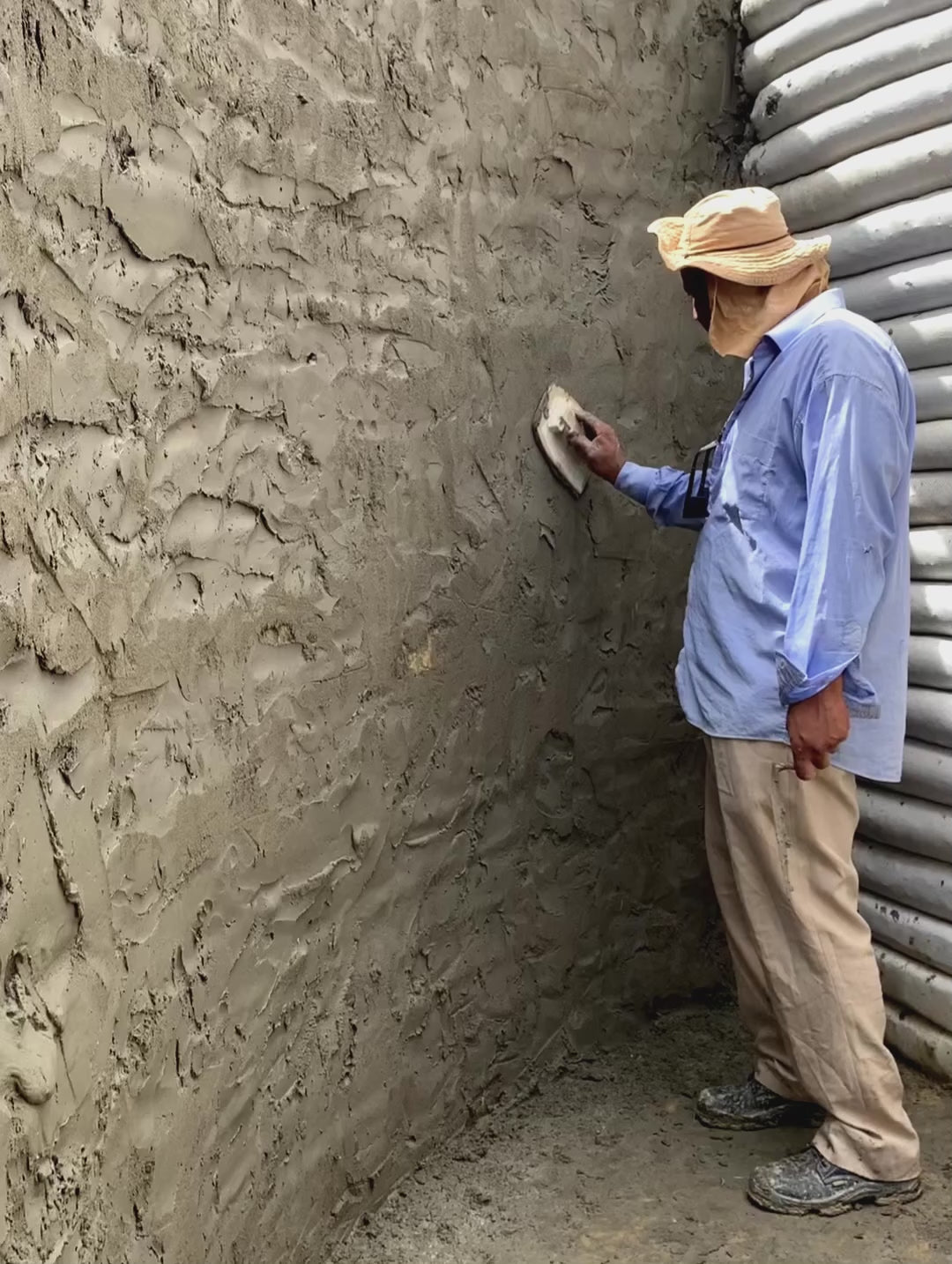
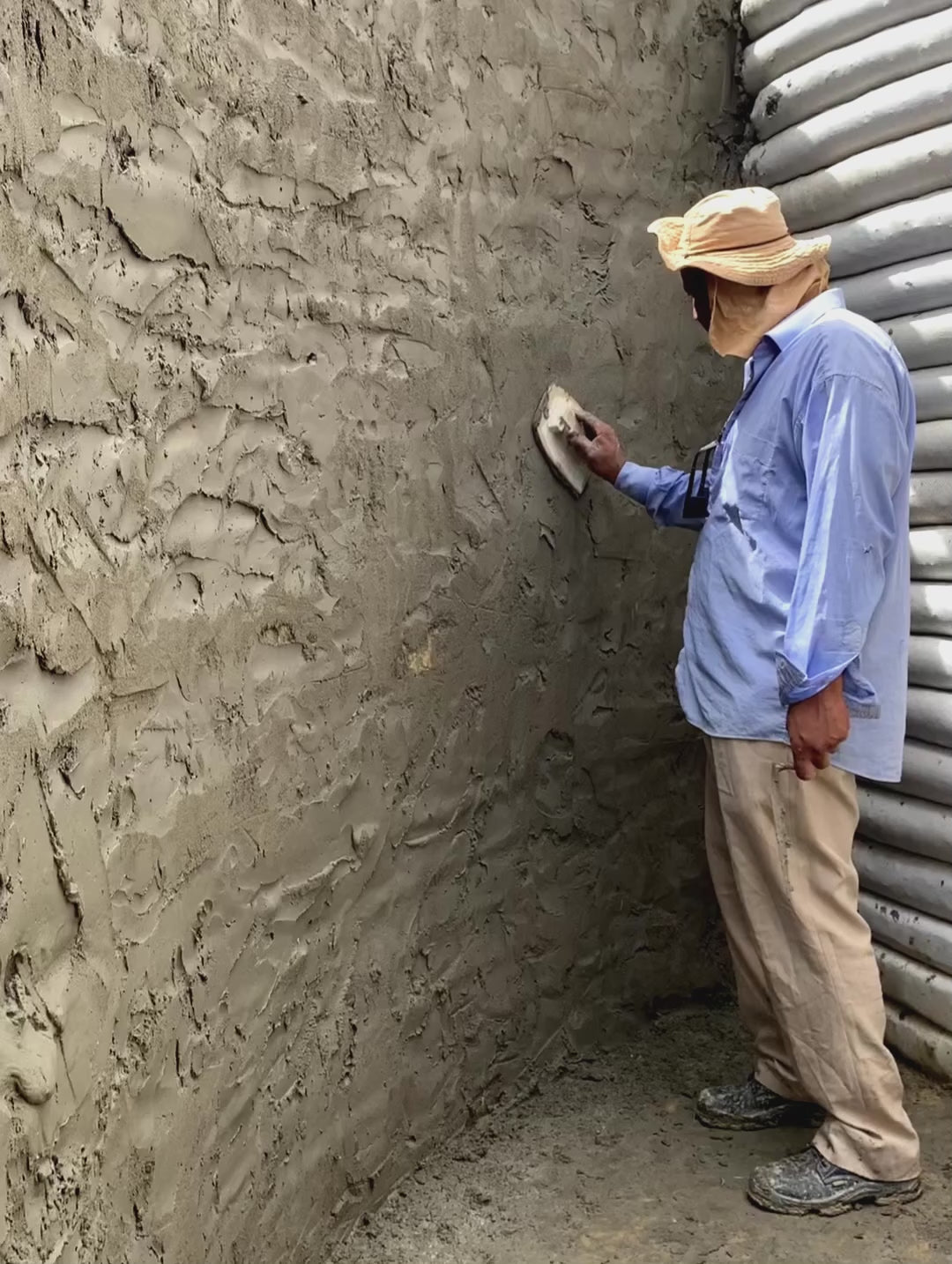
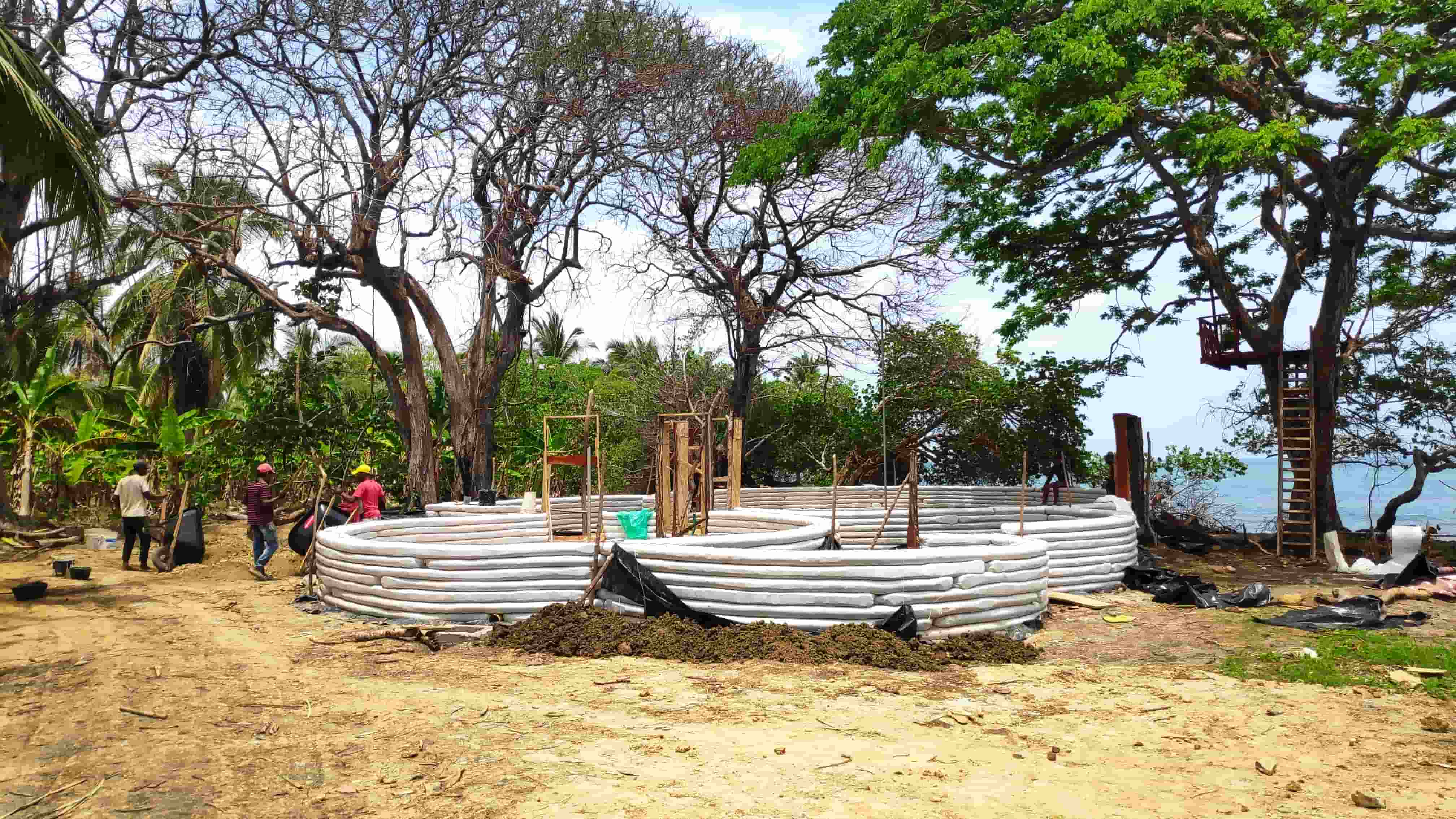
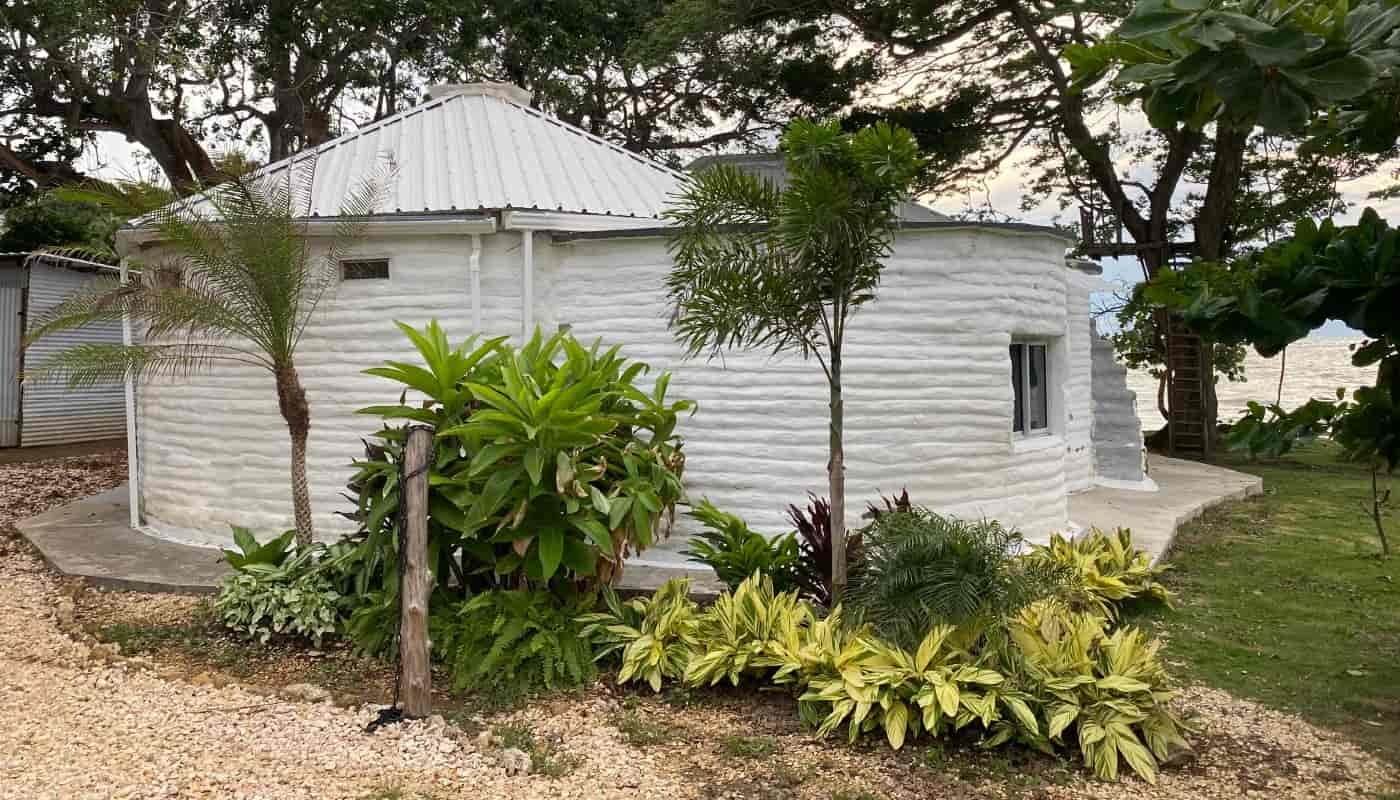
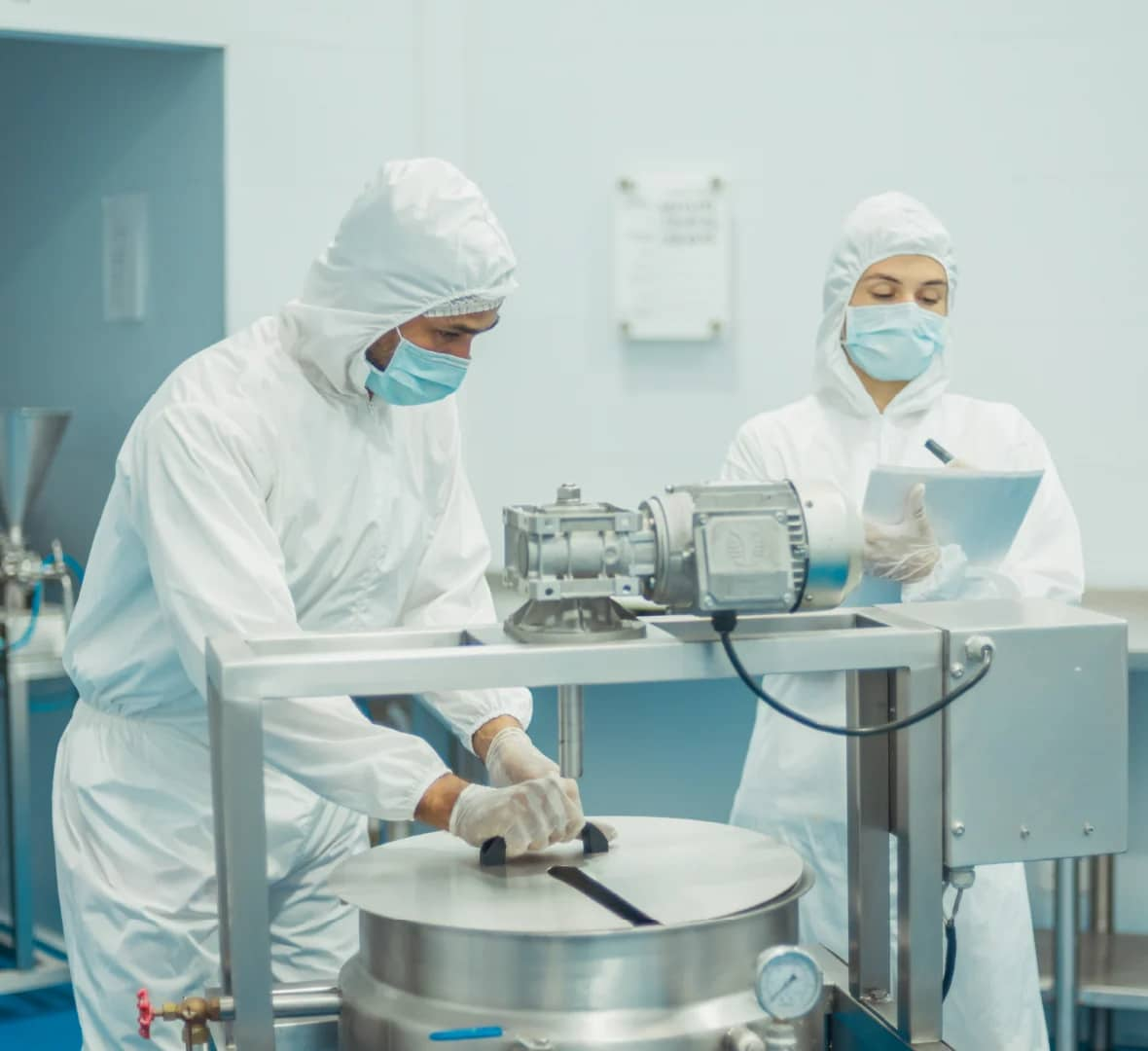
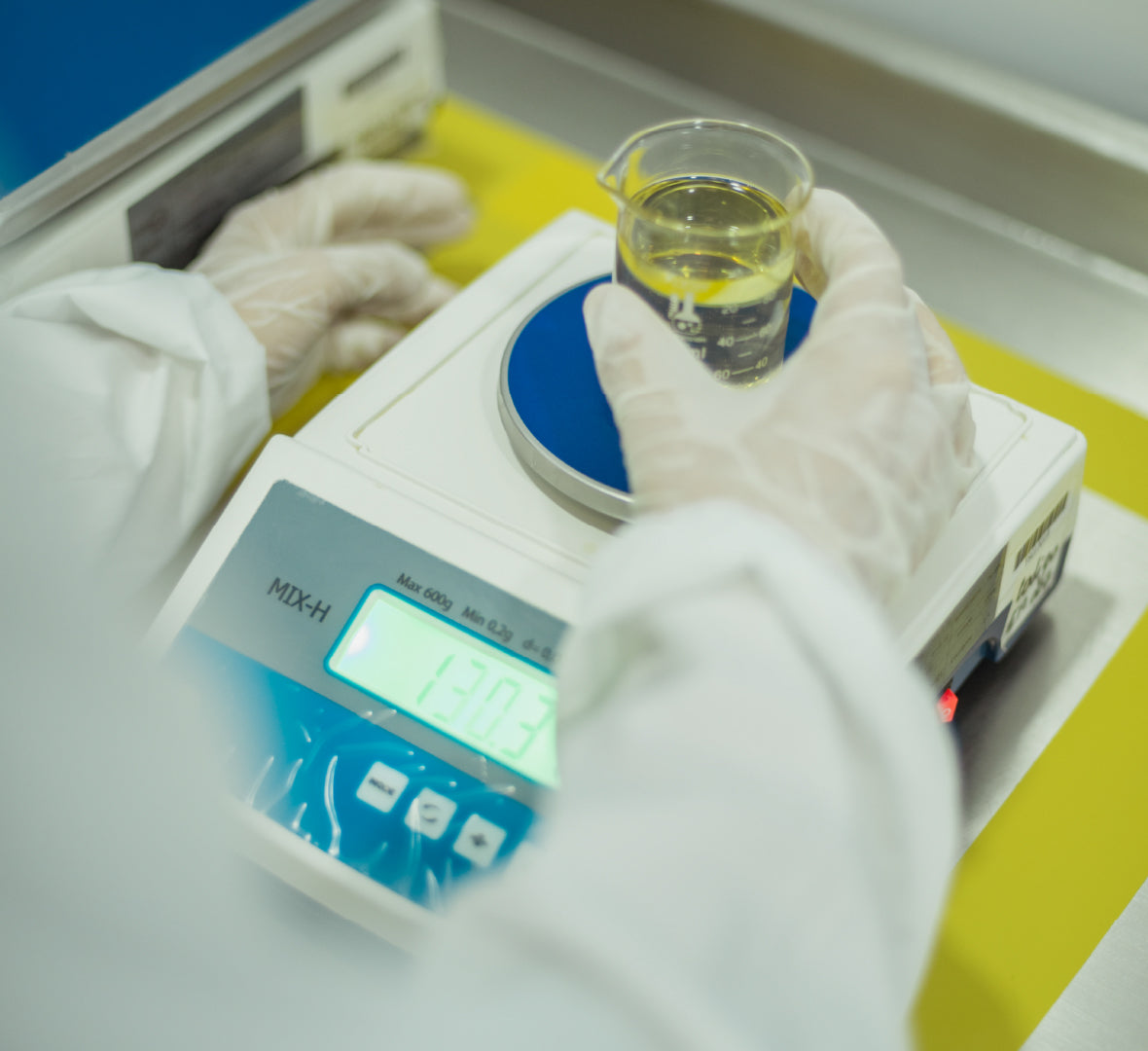

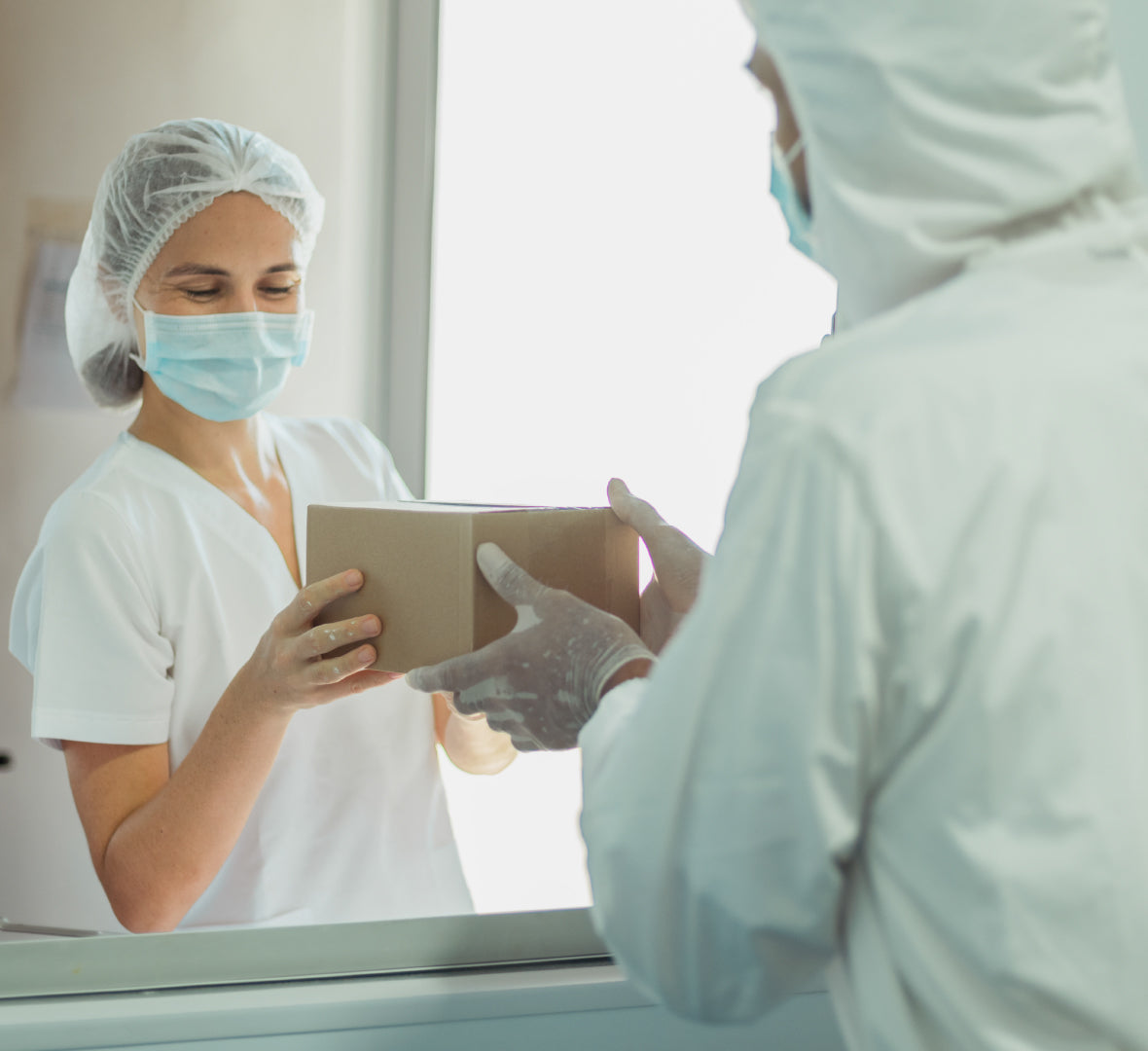